
Lennart Gorholt
Senior Director Sustainability at Phoenix Contact
Phoenix Contact is headquartered in Blomberg, Germany, and manufactures products and components for electrification, networking, and automation.
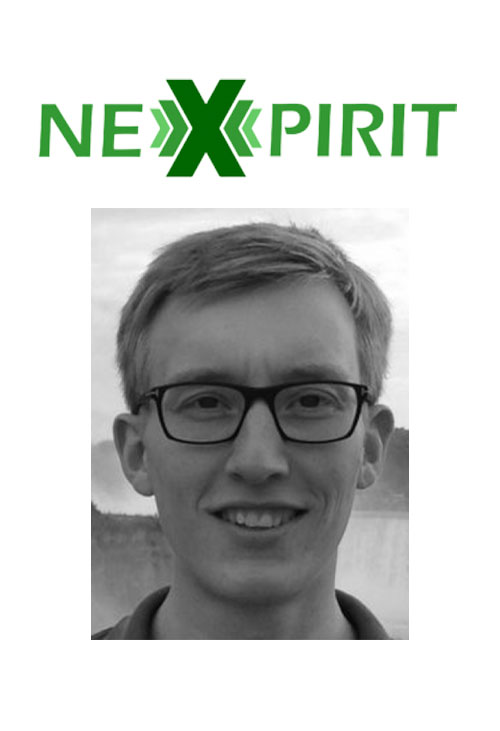
Lucas Dann
CEO and Co-Founder of Nexpirit GmbH, a Siemens Expert Partner specializing in the implementation of Teamcenter PLM. Nexpirit focuses on consulting and executing efficient material data management, successful material compliance, and the early integration of sustainability requirements into product development.
How Did Phoenix Contact and Nexpirit Come Together?
Lucas Dann: It all started during the COVID-19 pandemic when Phoenix Contact approached us to develop a sustainability solution for their products. Their goal was to contribute to climate neutrality wherever their products and components were used. This meant finding a way to systematically track the ecological footprint of approximately 10,000 materials and 100,000 products.
What was the main objective for Phoenix Contact?
Lennart Gorholt: As the person responsible for sustainability at Phoenix Contact, I focus on how we interpret and implement sustainability within our company. Our ultimate goal is to contribute to a more sustainable world, and we have set this as a standard across all 60 global subsidiaries.
What were the challenges in your project?
Lennart Gorholt: In the past, we mainly focused on lead times and costs. Now, we have to add a new dimension: the environmental impact of our products. Customers want to know the carbon footprint of a specific product before using it, for example, to calculate the total CO₂ consumption of a building. We have thousands of individual products, and it’s impossible to assess each one separately. Another challenge is that material compositions from suppliers frequently change, affecting the accuracy of our calculations.
How did you approach the solution?
„The earlier you start, the more freedom you have to make a good choice.“
Lennart Gorholt: First, it was about how the data is stored and made transparently available within the company so that smart decisions can be made. The second aspect was making sure these decisions are made as early as possible in the product lifecycle to keep costs and effort low. The third aspect was avoiding any manual data entry for the calculations.
Lucas Dann: Our solution was to integrate all necessary data into Teamcenter PLM. Teamcenter and NX are flexible and modular, allowing us to embed our sustainability solutions seamlessly. We enabled early CO₂ analysis in the design phase by assigning generic material data. For example, when selecting a specific type of steel, the system automatically provides a standard CO₂ value, allowing engineers to begin optimizing right away. Currently, we calculate 18 sustainability factors, including CO₂ emissions, water usage, and energy consumption.
How does your system work now?
Lennart Gorholt: We run automated calculations for products that are still in early development, fully developed products that are already on the market, and even for discontinued products to update their sustainability impact.
What are the biggest advantages for Phoenix Contact?
„The biggest advantages are scalability and automation.“
Lennart Gorholt: Previously, calculating the first carbon footprint took months. Now, we get results at the push of a button. This allows us to focus on what really matters: Where can we make the biggest impact on sustainability?
„The smarter the digital twin becomes, the better our environmental analysis will be.“
Lucas Dann: Another advantage is that the digital twin of our products is becoming more intelligent. With NX, we don’t just model geometry but also manufacturing processes. By integrating data from CAM (Computer-Aided Manufacturing) and supply chain emissions (Scope 3), we can further improve CO₂ calculations. The ability to manage everything in one system makes a big difference.
How will sustainable product development evolve in the future?
„In the Digital Product Passport, sustainability and environmental information, as well as material data, will play a central role.“
Lucas Dann: In the future, companies won’t just provide price and technical information—they’ll also have to disclose the environmental impact of their products. In Europe, this will be regulated through the Digital Product Passport, which will become mandatory in the coming years. AI will also play a role in automating sustainability assessments, for example, by estimating missing supplier data. However, ensuring transparency and reliability remains a challenge.
What advice would you give to companies on their sustainability journey?
„It’s about taking the first steps.“
Lennart Gorholt: If you wait for the perfect solution, you’ll wait forever. Just take the first steps and learn along the way.
„Sustainability must become an integral part of your company’s DNA“
Lucas Dann: Sustainability shouldn’t be seen as a burden—it’s an opportunity. It opens doors to new markets and differentiates you from competitors. Many industries, from automotive to construction, now require CO₂ data to even consider purchasing products. This trend will only grow. Start today by structuring your bills of materials (BOMs), collecting material data, running initial calculations, and optimizing from there.
Listen to the full conversation with Lucas and Lennart in the video: